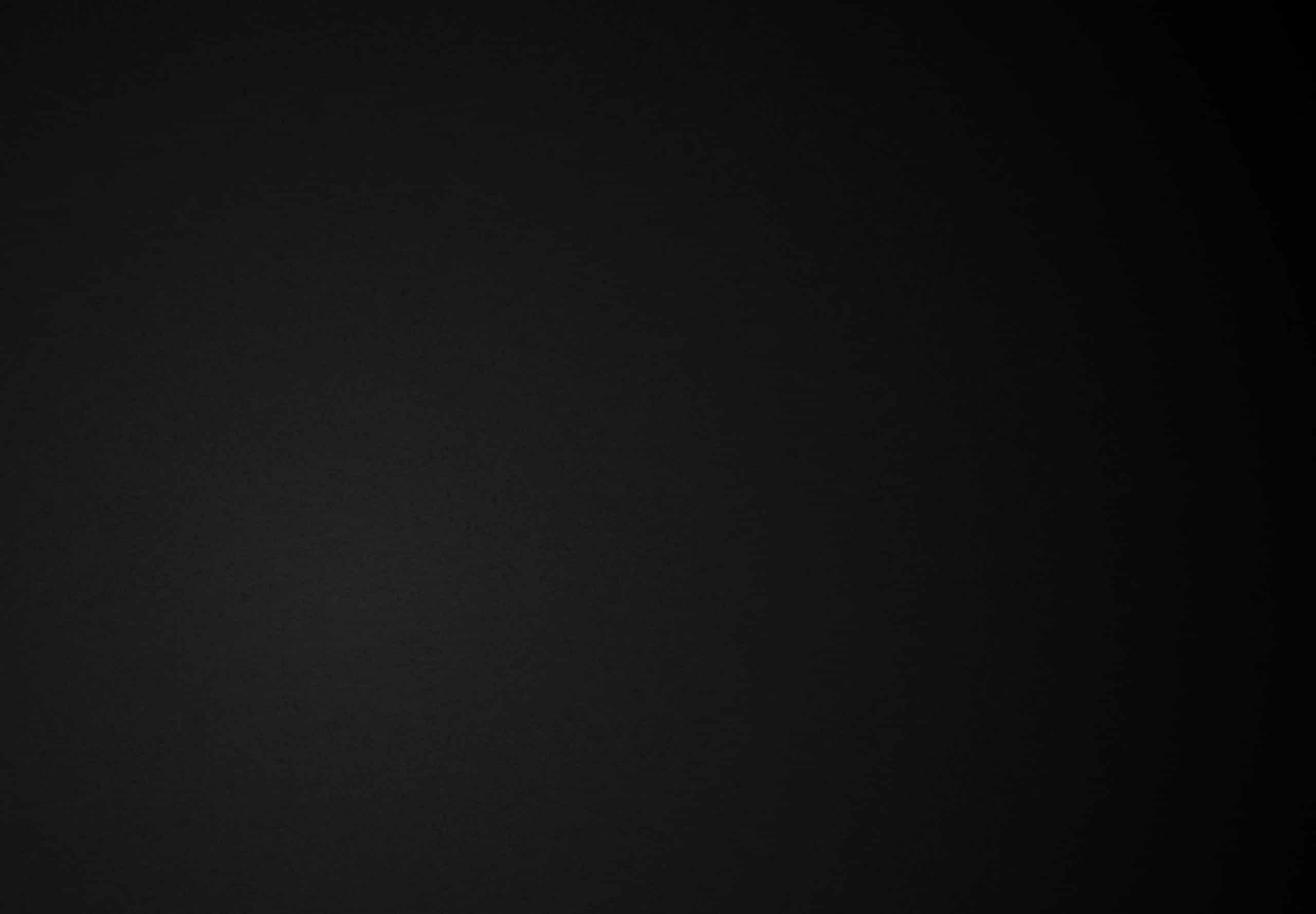
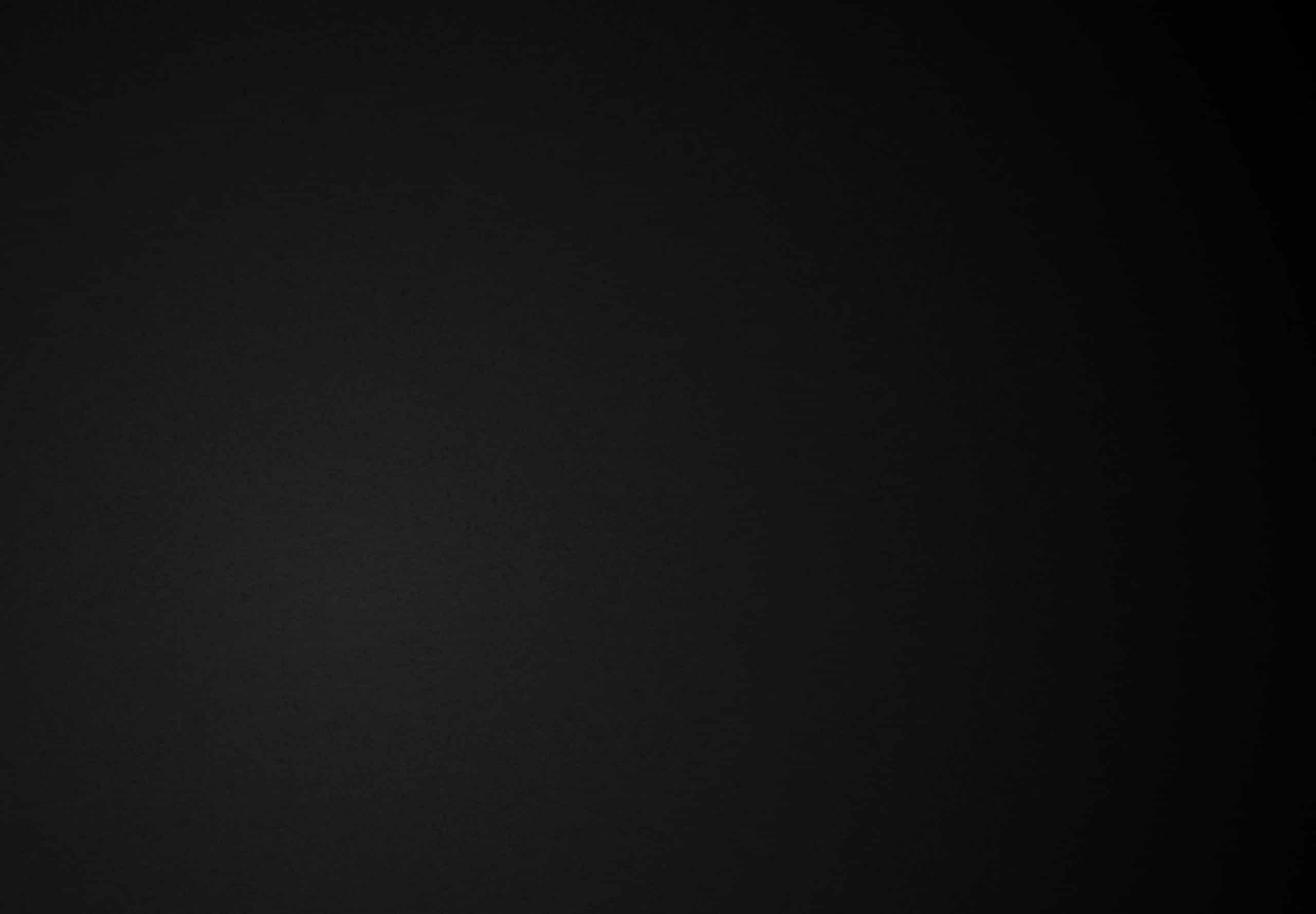
LAST UPDATED JUNE 26, 2023
Automation1 FAQ
Get answers to your most common Automation1 questions. Can’t find what you need here? Try the Automation1 help files or Contact Sales for more support.
What is the Automation1 Control Platform?
The Automation1 precision machine and motion control platform is a set of products and solutions that are combined to configure, develop and deploy precision automation and motion control systems. Automation1 is the most user-friendly platform available for precision motion control. The set of required products for any given Automation1 system depends upon the requirements of each application. The platform consists of:
-
Software for developing your application.
-
A controller for motion control and machine functionality.
-
Motor drives and controls for servo motors and laser scan heads.
-
A high-speed communication bus for connecting the controller and drives.
-
Several pieces of advanced automation technology available only from Aerotech.
Who uses the Automation1 platform?
Automation1 is used by anybody who requires precision motion control and automation — machine builders, researchers, process developers, manufacturers of all types, educators and even artists. Also, Automation1 is used in many many different industries. For this reason, Automation1 is built on a set of tools and technologies that can be applied creatively to address a wide variety of applications.
How do I build a motion control solution with Automation1?
Typically an Automation1 solution starts with picking the right motor drive or drives. This depends on the type of mechanical device you are controlling. Then the Automation1 controller is configured to meet the needs of the application. Most users begin by working with the software tools provided with the Automation1 Motion Development Kit (MDK). Automation1 can also be configured and programmed using one of Aerotech’s application programming interfaces.
How do I learn more about Automation1?
Aerotech.com provides information about Automation1. Here are some helpful links:
Which PC operating systems work with Automation1?
The Automation1 MDK and Automation1 iSMC work with Windows 10 on select PC’s. Automation1 2.7 and newer can be used with Windows 11 on select PC’s. The Automation1 .NET API is built on .NET Core, enabling users to build custom applications for both Windows and Linux operating systems. However, currently there is no Linux compiler for Automation1 AeroScript™ programs, so the Linux use case is limited.
Which industrial bus does Automation1 support?
For more information, please refer to the Motion Controller Selection Guide.
How do I try Automation1?
Aerotech offers a complementary basic installation of the Automation1 MDK. Find your local field sales engineer to get access to Automation1.
How do I install and activate Automation1 on My PC?
Please see the Automation1 help files for more information.
How does installing Automation1 affect My PC?
Installing the Automation1 MDK is like installing other Windows-based applications on your computer. The iSMC installation requires an installation of a real-time operating system (RTOS), which enables your PC with the extremely high deterministic behavior required for precision motion control. Please see the Automation1 help files for more information.
What is Automation1 software and what does it do?
The most user-friendly interface available for precision motion control, Automation1 software is referred to as the Automation1 Machine & Motion Development Kit (MDK). In many cases, using the Automation1 MDK reduces your setup time from days to minutes. The MDK software tools include a studio application, status utility, console application, help files, C API, Python API and .NET API. For more information, please refer to the Automation1 MDK website.
Can I start using Automation1 software before I have the hardware?
Yes. The Automation1 studio application includes a development mode called ‘virtual mode’. You are able to set up and configure virtual axes. These virtual axes are treated like connected servo motor drives, allowing programmers to develop their application code, compile and run this code, and even visualize simulated feedback from the actual commanded motion. For more information, please refer to the Automation1 MDK and the Automation1 iSMC websites.
Does Automation1 Have a Software Tool for Creating an HMI?
Yes, the Automation1 MachineApps HMI Builder for Windows PCs enables users to quickly develop custom, effective HMI screens for your precision machine or motion system with varying levels of access control.
What are the PC requirements for installing the Automation1 MDK software?
Please see the Automation1 PC Selection Guide for more information.
What is the Automation1 controller?
The Automation1 Intelligent Software-Based Motion Controller (iSMC) converts commands programmed in the AeroScript language or the Automation1 APIs into commands that can be executed upon by Automation1 drive hardware. For more information, please refer to the Automation1 iSMC website.
Does the Automation1 controller have the features my system requires?
Please see the Motion Controller Selection Guide for a detailed feature comparison between Automation1 and Aerotech’s other controller platforms. If a feature you are interested in does not exist on that page, please contact us with your question and we will respond quickly with an answer.
How do I program the Automation1 iSMC controller?
The controller can be programmed using the AeroScript programming language, which includes RS-274 G-Code support (see below), or one of Aerotech’s APIs. For more information, please refer to the Automation1 iSMC website.
How do I connect Automation1 drives and drive racks to my controller?
Automation1 drives and drive racks are connected via the HyperWire communication network. For more information, please refer to the Automation1 HyperWire website.
What are the PC requirements for installing the Automation1 iSMC controller?
Please see the Automation1 help files for more information.
What are Automation1 drives and drive racks and what do they do?
Automation1 drives and drive racks are electronic devices containing digital controllers, power amplifiers and input/output (I/O) connection points. They are designed for controlling one or several servo motors, precision stages, galvo scan heads or hexapods.
Which drives and drive racks are available with Automation1?
A complete listing of available and future drives and drive racks can be found on the Motion Controller Selection Guide.
If I currently have a system with an A3200 motion controller communicating to Automation1 drives and/or drive racks (over HyperWire) do I need to order new drives in order to migrate from A3200 to Automation1?
No. Automation1 drives and/or drive racks which are on a motion system with an A3200 motion controller can have their firmware migrated to Automation1 firmware when migrating to the Automation1 motion controller. Please see the Automation1 help files for more information.
What is safe torque off (STO) and which Automation1 drives have this safety feature?
STO is an integrated servo drive safety feature. The STO function ensures that no torque can act upon the motor. It does this by blocking electrical signals from the drive to the motor. The STO circuit consists of two identical channels, each of which must be energized for the servo drive to produce motion. Each STO input is opto-isolated and accepts 24V levels directly without the need for external current limiting resistors. Aerotech’s STO implementation allows maximum achievable safety ratings of safety integrity level (SIL) 3 and category four performance level (PL)e. Most Automation1 servo motor drives include this feature. Please refer to each drive’s respective hardware manual for more information.
Do Automation1 drives have additional safety features?
Most Automation1 servo motor drives include a fail-safe brake output and the option for an external shunt resistor. Each drive communicates faults, including E-stop conditions to the Automation1 controller, enabling the controller to manage system level safety. Additionally, each drive can be programmed to respond to “safe zones” specified by the Automation1 controller. Safe zones prevent motion either into or out of one or multi-dimensional regions. You can have a maximum of 32 safe zones.
Do Automation1 drives support absolute encoders?
Yes. All Automation1 servo motor drives support absolute encoder feedback with their base configuration. Please refer to each drive’s respective hardware manual for more information.
Which certifications exist for the drive hardware?
All Aerotech drive hardware is CE approved, holds Nationally Recognized Testing Laboratory (NRTL) safety certification and is EU 2015/863 RoHS 3 compliant. For more information, please refer to Aerotech’s drives and drive racks page.
Which communication bus does Automation1 use?
For communicating trajectory and process control information between drives and the controller, Automation1 exclusively supports the HyperWire fiber-optic, light-based motion control bus. HyperWire is the fastest, highest-throughput communication bus in motion control. It enables 20 times the throughput than 100BASE-T Ethernet. Automation1 also supports several methods of communication between the controller and other applications. The Automation1 MDK software and the various API tools it provides can communicate with the Automation1-iSMC controller over Ethernet or USB. The controller also supports EtherCAT and Modbus Industrial Ethernet communication protocols and a simple Ethernet TCP/IP socket interface.
Is special hardware required for HyperWire?
Aerotech’s HyperWire bus requires the HyperWire PCIe card and HyperWire fiber-optic cable. HyperWire cables are active-optical, glass-optical-fiber cables with small form-factor pluggable (SFP) connectors on each end.
How do Automation1 drives and drive racks connect with HyperWire?
Drives and drive racks are connected to the HyperWire network via HyperWire cables (see above). The connection is a line-style connection. The HyperWire-PCIe card has an A and a B port, each supporting 16 axes for a total of 32 axes on an Automation1 motion control network.
Does Automation1 support other communication buses?
The Motion Controller Selection Guide identifies the ways you can communicate with an Automation1 control system.
Which programming languages does Automation1 support?
Automation1 supports the new AeroScript programming language for directly programming the controller from the Automation1 studio application. You can also choose to use one of our Automation1 APIs. See the Motion Controller Selection Guide for more information on Automation1 APIs.
What is AeroScript and how is it different from AeroBasic?
AeroScript is Aerotech’s new programming language, available with the Automation1 motion control platform. It offers dramatic improvements in accessibility and functionality. Developers will enjoy modern programming language features such as syntax autocompletion and code snippets. They will also enjoy improved readability and portability of their programs. Refer to the AeroScript Equivalents of AeroBasic Commands for the A3200 and AeroScript Equivalents of AeroBasic Commands for the Ensemble and Soloist help files for more information.
Do I need to migrate my controller from A3200 to Automation1?
All new systems should be built on the Automation1-iSMC intelligent software-based motion controller with the Automation1-MDK motion development kit. All A3200 products are non-current and not available for use on new designs. Please contact Global Technical Support for information on A3200 products.
For existing A3200 systems using Ndrive, Npaq, Nservo, Nstep, or Nmark (Firewire) drives, all customers should develop a migration path that includes updating these drives to new Automation1 (HyperWire) drive hardware. Having a plan in place for upgrading all drives and controller software to Automation1 equivalent products is recommended. If Automation1 equivalent drives are available and supported in A3200 version 6.04 software (see table below), it is possible to upgrade electronics only to Automation1 and continue using the A3200 motion controller. Please consult with your local field sales engineer.
A3200 systems built on Automation1 HyperWire drives can continue to run A3200 version 6.04 controller software. However, it is recommended to have a migration plan developed and ready to execute in the event that Windows and Intel support dictates that a migration is required. To begin your navigation plan, please consult your local field sales engineer and refer to some of the migration tools we have in the Automation1 Help Files.
Do I need to migrate my controller from Ensemble/Soloist to Automation1?
All Ensemble and Soloist products are non-current and not available for use on new designs. Please contact Global Technical Support for information on Ensemble and Soloist products. All new systems should be built on the Automation1-iSMC intelligent software-based motion controller with the Automation1-MDK motion development kit. Aerotech does not recommend any new designs to use Ensemble or Soloist products. Existing Ensemble/Soloist systems do not have Automation1 equivalent drives that are supported by any version of the Ensemble or Soloist controllers (see table below). Therefore, a plan should be in place to migrate the system’s full control architecture (controller, motion bus and drives) to Automation1. To begin your navigation plan, please consult your local field sales engineer and refer to some of the migration tools we have in the Automation1 Help Files.
What is the process for migrating from A3200 to Automation1?
Please see the Automation1 help files for more information.
Will my AeroBasic programs work with Automation1?
AeroBasic programs are not directly supported by Automation1. Automation1 includes a new programming language called AeroScript. AeroScript includes G-Code support, so motion commands programmed in G-Code syntax will be supported in Automation1. However, the AeroBasic syntax in many A3200, Ensemble and Soloist program files will not compile in Automation1.
How do I convert my programs from AeroBasic to Automation1?
To assist in migrating your AeroBasic programs to AeroScript, use the AeroBasic To AeroScript Tool. For instructions, see the question above, „What is the process for migrating from A3200 to Automation1?“ For more help, the Automation1 help file includes the topic AeroScrip Equivalents to AeroBasic Commands.
Does Automation1 have drives and drive racks that are equivalent to my A3200 products?
Yes. Most A3200 products have “drop-in replacements” in Automation1. You get the benefit of improved performance without the hassle of redesigning your machine layout. Please refer to the following table:
Product Type | A3200 Product | Non-Current Date(1) | Automation1 Equivalent | Supported in A3200 Version 6.04-Current |
---|---|---|---|---|
Development Software | A3200 Motion Composer Suite & A3200 Software-Based Machine Controller |
June 30, 2023 – All versions 4.x & 5.x December 29, 2023 – All versions 6.x |
Automation1 MDK | n/a |
Motion Controller | Automation1 iSMC | n/a | ||
HMI Software | A3200 CNC Operator Interface | Automation1 MachineApps | n/a | |
A3200 Motion Simulator | n/a | |||
Trajectory Design Software | A3200 Motion Designer | n/a | n/a | |
Industrial PC | A3200 iPC | December 29, 2023 | Automation1 iPC | Yes |
Drive Racks | Npaq | December 31, 2020 | Automation1 XR3 | Yes |
Npaq MR | June 30, 2023 | |||
Npaq 6U | December 31, 2020 | |||
PWM Servo Drives | Ndrive HPe (50/75/100/150/200 Amp) | December 29, 2023 | Automation1 XC6e | No A3200 Support |
Ndrive HPe (10/20/30 Amp) | August 31, 2021 | Automation1 XC4e | Yes | |
Ndrive CP | August 31, 2021 | Automation1 XC4 | Yes | |
Automation1 XA4-AC | No A3200 Support | |||
Ndrive MP | June 30, 2023 | Automation1 XC2e | No A3200 Support | |
Automation1 XC2 | Yes | |||
Automation1 XA4-DC | No A3200 Support | |||
Linear Servo Drives | Ndrive HLe | December 29, 2023 | Automation1 XL5e | No A3200 Support |
Ndrive ML | December 29, 2023 | Automation1 XL2e | No A3200 Support | |
Galvo Scan Head Drives | Nmark GCL | December 29, 2023 | Automation1 GL4 | Yes |
Nmark CLS | June 3, 2016 | |||
Multi-Axis Robotic Controller | HEX RC | June 30, 2023 | Automation1 XR3 | Yes |
Piezo Nanopositioner Drives | Ndrive QLe | August 8, 2022 | n/a | No A3200 Support |
Ndrive QL | August 8, 2022 | n/a | No A3200 Support | |
Clock & Direction (Stepper) Interface | Nstep | December 29, 2023 | Automation1 SI4 | No A3200 Support |
Analog Command (Servo) Interface | Nservo | December 31, 2021 | Automation1 XI4 | No A3200 Support |
Galvo Scan Head XY2-100 Interface | Nmark SSaM | December 29, 2023 | Automation1 GI4 | No A3200 Support |
(1) Non-current products are discontinued and are no longer sold and marketed through normal Aerotech channels. The product may be available for purchase through our Global Technical Support Group but availability may be unreliable. A product moves to obsolete status once we are no longer able to manufacture the product.
(2) Not yet available.
What HyperWire parts should I be ordering to replace my FireWire bus?
See the table below.
Product Type | A3200 Product | Automation1 Equivalent |
---|---|---|
PCI Card | NFIRE PCI | n/a(1) |
PCIe Card | NFIRE PCIe | HyperWire PCIe |
Communication Cables | NCONNECT 6P6P-xx(2) | HyperWire AO10-xx(2) |
HyperWire Network Repeater | NFIRE RPTR-1394A-1394A | Not required |
(1) Currently there is no PCI version of the HyperWire card.
(2) Whereas “xx” designates the length in decimeters.
Is there a way to connect A3200 drive hardware to an Automation1 controller?
Automation1 does not support the FireWire-based motion bus used by A3200 drives. Automation1 uses a new fiber-optic bus called HyperWire. There is no FireWire-to-HyperWire conversion tool or product, so A3200 drives cannot connect to a HyperWire network or Automation1 controller.
Does Automation1 have drives and drive racks that are equivalent to my Ensemble and Soloist products?
Yes. Aerotech is currently releasing Ensemble and Soloist drive hardware “drop-in replacements” in Automation1. You get the benefit of improved performance without the hassle of redesigning your machine layout. Note: Automation1 equivalent products are not supported in the Ensemble or Soloist platforms. You must switch your motion controller to the Automation1-iSMC in order to use these Automation1 products. Please refer to the following table:
Product Type | Ensemble/Soloist Product | Non-Current Date(1) | Automation1 Equivalent |
---|---|---|---|
Development Software | Ensemble – Includes the Ensemble Motion Composer Suite | December 29, 2023 | Automation1 MDK |
Soloist – Includes the Soloist Motion Composer Suite | December 29, 2023 | ||
Motion Controller | Ensemble Multi-Axis Drive-Based Motion Controller | December 29, 2023 | Automation1 iSMC |
Soloist Multi-Axis Drive-Based Motion Controller | December 29, 2023 | ||
Trajectory Design Software | Ensemble Motion Designer | December 29, 2023 | n/a |
Soloist Motion Designer | December 29, 2023 | ||
Drive Racks | Epaq | December 29, 2023 | Automation1 iXR3(5) / Automation1 XR3 |
Epaq MR | December 29, 2023 | ||
PWM Servo Drives | Ensemble HPe (50/75/100/150/200 Amp) | December 29, 2023 | Automation1 iXC6e(5) / Automation1 XC6e |
Soloist HPe (50/75/100/150/200 Amp) | December 29, 2023 | ||
Ensemble HPe (10/20/30 Amp) | February 15, 2022 | Automation1 iXC4e(5) / Automation1 XC4e | |
Soloist HPe (10/20/30 Amp) | February 15, 2022 | ||
Ensemble CP | February 15, 2022 | Automation1 iXC4(5) / Automation1 XC4 / Automation1 XA4 | |
Soloist CP | February 15, 2022 | ||
Ensemble MP | December 29, 2023 | Automation1 iXC2e(5) / Automation1 XC2e Automation1 iXC2(5) / Automation1 XC2 |
|
Soloist MP | December 29, 2023 | ||
Linear Servo Drives | Ensemble HLe | December 29, 2023 | Automation1 iXL5e(5) / Automation1 XL5e |
Soloist HLe | December 29, 2023 | ||
Ensemble ML | December 29, 2023 | Automation1 iXL2e(5) / Automation1 XL2e |
|
Soloist ML | December 29, 2023 | ||
Lab Controller | Ensemble LAB | March 31, 2022 | n/a(3) |
Piezo Nanopositioner Drives |
Ensemble QLe | August 8, 2022 | n/a |
Ensemble QL | August 8, 2022 | n/a | |
Ensemble QDe | March 31, 2022 | n/a(3) |
|
Ensemble QLAB | March 31, 2022 | n/a(3) | |
Analog Command (Servo) Interface | n/a(4) | n/a(4) | Automation1 iXI4(5) / Automation1 XI4 |
(1) Non-current products are discontinued and are no longer sold and marketed through normal Aerotech channels. The product may be available for purchase through our Global Technical Support Group, but availability may be unreliable. A product moves to obsolete status once we are no longer able to manufacture the product.
(2) Not yet available.
(3) No Automation1 equivalent product planned.
(4) Did not exist in the Ensemble or Soloist motion control platforms.
(5) This device gets the Automation1 iSMC installed on it, becoming a motion controller in addition to a drive product.
What is the plan moving forward for the A3200 motion control platform?
As a non-current product, the A3200 software and controller will continue to be sold and supported by Aerotech’s Global Technical Support team for years to come. A3200 software and controller support is tied to the support of the Windows 10 OS. Please see the Microsoft website or reach out to our Global Technical Support team for questions on Microsoft Windows 10 support.
A3200 drive products will be manufactured and serviced as long as Aerotech can source components.
Starting in 2024, Aerotech’s Global Technical Support (GTS) team is exclusively responsible for selling and servicing A3200 products.
What is the plan moving forward for the Ensemble and Soloist motion control platforms?
As a non-current product, the Ensemble and Soloist software and controller products will continue to be sold and supported by Aerotech’s Global Technical Support team for years to come. The Ensemble and Soloist software and controller will continue to be sold and supported for as long as hardware support can be maintained for the Ensemble and Soloist drive products. Because the Ensemble and Soloist have hardware-based controllers, the longevity of the Ensemble and Soloist hardware will determine the longevity of the control platform. Because Ensemble and Soloist software runs on Windows 10, these tools will be supported as long as a branch of Windows is actively supported. Please see the Microsoft website or reach out to our Global Technical Support team for questions on Microsoft Windows 10 support.
Starting in 2024, Aerotech’s Global Technical Support (GTS) team is exclusively responsible for selling and servicing Ensemble and Soloist products.
What happens if a legacy drive or drive rack product (an A3200 Firewire, an Ensemble, or a Soloist drive or drive rack) fails and is no longer available?
If a legacy drive product fails and cannot be repaired or replaced by our Global Technical Support team, Aerotech will still support your needs. First, we can evaluate if another legacy drive product can be used in its place.
If not, for A3200 Firewire drives, it is possible that an Automation1 drive product replacement will work to replace your A3200 drive. A subset of Automation1 drives also works with the 6.x version of the A3200 controller. All drives in your control system would then need to be Automation1 drives for this solution to work, as the FireWire and HyperWire networks cannot be used together.
If another legacy drive cannot be used for Ensemble and Soloist drives, all drives in your control system would then need to be Automation1 drives for this solution to work, which would require a complete migration to the Automation1 iSMC controller, Automation1 drive hardware and the HyperWire drive-to-drive communication bus (Ensemble only).
Finally, for A3200 systems, if the required replacement Automation1 drives are not supported in A3200 version 6.04, your entire control system – drives, motion bus and controller – must be migrated to Automation1.
How long will I be able to purchase legacy drive hardware?
Aerotech will sell and service all legacy drive products as long as we can source components to make these products.
Will Aerotech continue to offer phone and email support for legacy products?
Yes. Even as Automation1 becomes the preferred option, the A3200, Ensemble and Soloist motion control platforms will be supported by Aerotech’s Global Technical Support team.
How does Microsoft’s support of Windows 10 affect Aerotech’s support of A3200?
When Microsoft drops support for an operating system (OS), that OS will stop getting critical security upgrades. Our users must identify and plan for any risks that result from maintaining an industrial control system on a PC with an insecure OS. This will be a critical aspect of each user’s evaluation when determining a timeline to maintain and operate A3200 motion control systems. This is because the A3200 will not support the next Microsoft operating system. Please see the Microsoft website or reach out to our Global Technical Support team for questions on Microsoft Windows 10 support. For Windows 11 support, please look to migrate to Automation1.
Convert HyperWire & Drive Hardware from A3200 to Automation1
The following instructions assume that you are starting with a motion system based on:
- A PC with the A3200 software-based machine controller installed.
- The PC has a HyperWire card installed with A3200 firmware on the HyperWire card.
- The drives on your system are Automation1 drives with A3200 drive firmware installed, enabling those Automation1 drives to communicate to the A3200 controller over HyperWire.
Follow these steps to convert the HyperWire card and Automation1 drives to Automation1 firmware:
- Connect and power the drives that you wish to convert from A3200 to Automation1. Using the A3200 firmware loader, make sure that the HyperWire card and Automation1 drives have the same firmware on them.
- Download the A3200toAutomation1.zip file and save the „A3200-to-Automation1-2.4.1.loda“ and „Load Automation1 Firmware.bat“ files to your PC.
- Open A3200 Firmware Loader and ensure that all of the drives that you want to convert are listed.
- Use A3200 Firmware Loader to load A3200-to-Automation1-2.4.1.loda onto the drives. Verify that no error messages are printed in A3200 Firmware Loader.
- Completely uninstall the A3200 from your computer.
- Install the Automation1 MDK and Automation1 iSMC versions 2.0.0 or later.
- Download Load Automation1 Firmware.bat to your Desktop.
- Double-click Load Automation1 Firmware.bat. Follow the instructions in the window that pops up. Here is the output that you should see when you run Load Automation1 Firmware.bat:
Convert HyperWire and Drive Hardware from Automation1 to A3200
- Connect and power the drives that you wish to convert from Automation1 to A3200.
- If the current version of Automation1 is not 2.0.0 or later, install that version. The following steps will not succeed if a version prior to 2.0.0 is used.
- Using the Machine Setup tool in the Automation1 Studio application, ensure that HyperWire and drive firmware has been updated to match the version of the Automation1 iSMC controller.
- Download Automation1toA3200.zip and extract „Automation1-to-A3200-6.04.008.a1update“ and „Convert to A3200 Firmware.bat“ to your PC.
- Double-click Convert to A3200 Firmware.bat on your Desktop. Follow the instructions in
the window that pops up. Here is the output that you should see when you run Convert toA3200 Firmware.bat:
- Completely uninstall the Automation1 MDK and Automation1 iSMC from your computer.
- Install the A3200. Refer to the A3200 Help Files located at Manuals, Help Files & Cable Drawings page.
- Open the A3200 Firmware Loader and ensure that all of the drives that you want to convert are listed.
- Use A3200 Firmware Loader to load the default firmware on to the drives. Verify that no error messages are printed in A3200 Firmware Loader.
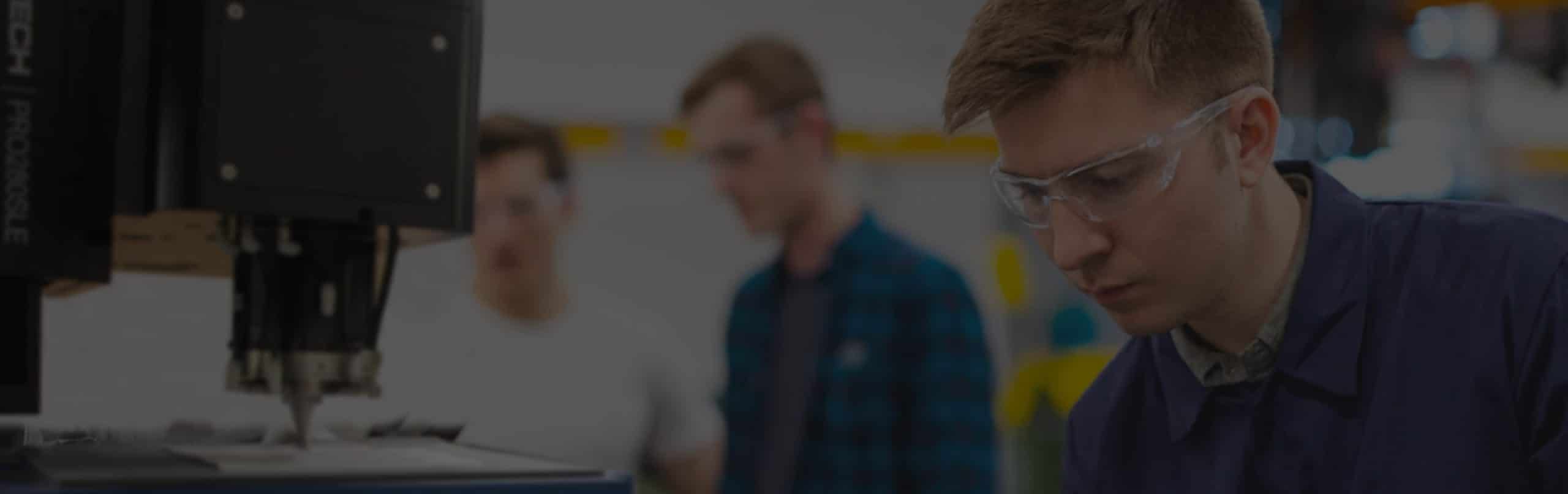
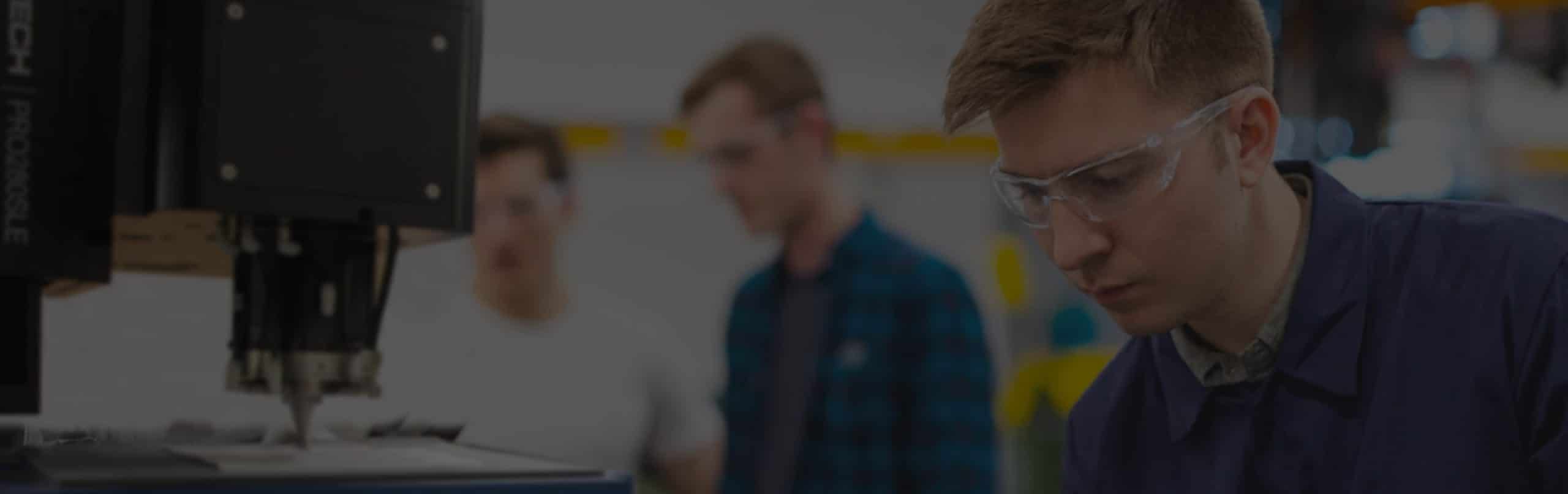