Application Note, Custom Engineered Motion Systems, Data Storage, Electronics, Gantries, Integrated Automation Systems, Laser Systems, Motion Control Platforms, Precision Manufacturing, Science & Research Institutions, Semiconductor, Stages & Actuators
Application Note
Implementation of the Enhanced Throughput Module (ETM) to Improve Machine Throughput
Due to the continuously increasing demand for consumer electronics, electronic equipment manufacturers are pushing the throughput limits of the equipment they build. UPH (unit per hour) is being challenged every time there is a new manufacturing machine developed. In this Application Note, Aerotech used our Enhanced Throughput Module (ETM) to reduce move and settle time and maximize throughput on a machine without changing the mechanical structure or the machine base design.
Introduction
Aerotech’s ETM is used to:
- Decrease settle time of point-to-point moves
- Increase throughput of existing and new machines
- Reduce undesirable effects of frame motion on servo systems
- Improve contouring performance
ETM improves positioning performance of high-dynamic motion systems by measuring and compensating for unwanted motion of the machine frame. This feature includes both a software and hardware sensor package that can measure and compensate for low frequency base motion.
Unwanted base motion occurs when a stage is accelerating, for instance when a motion axis is commanded to move. Newton’s third law states, “For every action, there is an equal and opposite reaction.” Our action is the stage acceleration; the reaction is the force imparted to the machine base. This reaction creates an oscillation in the machine base that affects the settling time of the stage axis. Accurate positioning during high-dynamic motion requires the controller to wait for this oscillation to settle before continuing with the process. The best solution is an optimized machine base, but this is expensive. However, in many cases ETM can be added to an existing machine to improve performance without structural changes to the machine, saving considerable time and cost while achieving significant improvements in throughput.
Mounting the ETM
ETM should be mounted in the direction of motion of the stage, but does not require precision alignment. The user can adjust the tuning gain of the ETM to compensate when the ETM is misaligned.
Sensor Display
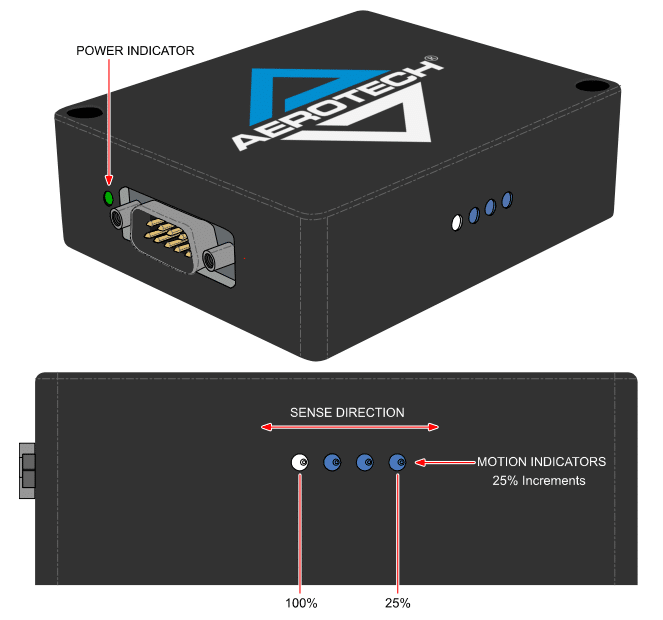
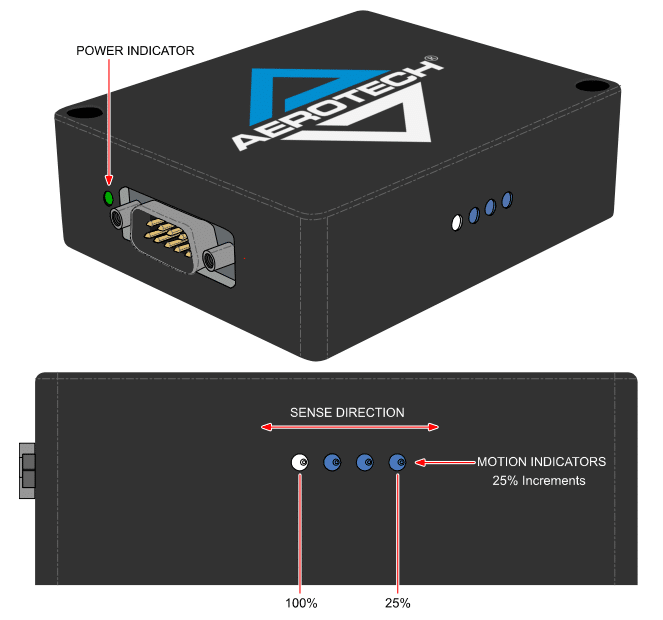
The blue LED display is a bar graph display indicating motion in 25% increments from 0% thru 100% (Figure 1).
Test Setup and Parameters
The test setup is based on a precision linear-motor-driven stage mounted to a granite base. The stage is set to make a 20 mm move at a speed of 282 mm/s. Move and settle time is 210 ms. We set the in-position stability requirement as 0.5 µm for 5 ms. We then plotted the position command, position error, and velocity command.
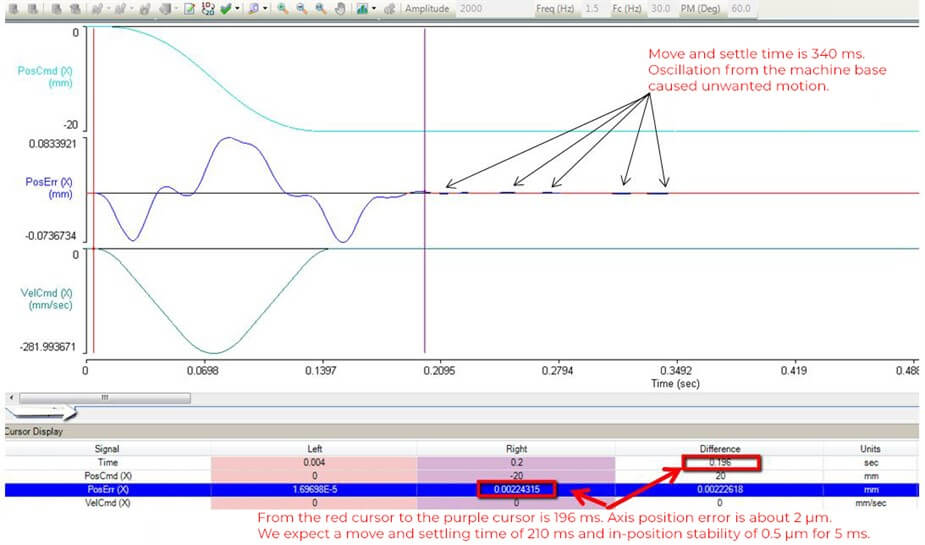
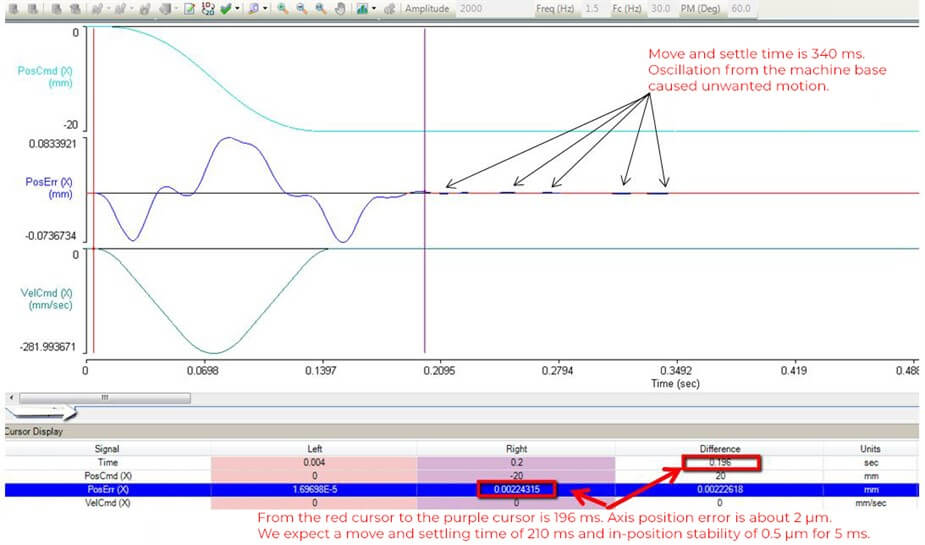
Servo Motion without ETM
Figure 2 shows the results of motion without ETM. Remember that we set our linear X axis to move 20 mm at 282 mm/s, with a required in-position stability of 0.5 µm for 5 ms. After the X axis completes the move, the blue color in the plot indicates that in-position error is over 0.5 µm. Also, the move and settle time is 340 ms. You can zoom-in at the end of the move, using the cursors, to measure the peak-to-peak position error of one well-defined oscillation. It is shown to be a 38 Hz oscillation due to the machine frame (Figure 3).
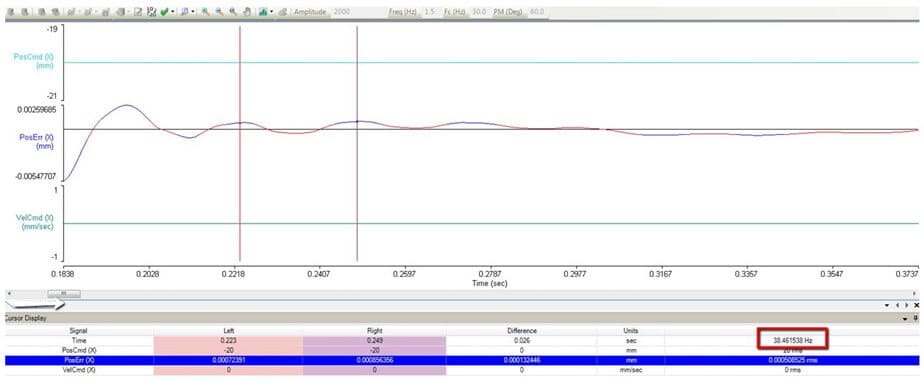
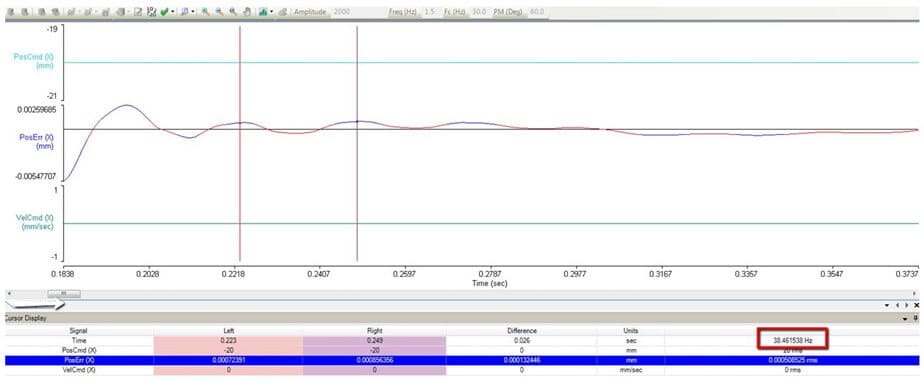
Servo Motion with ETM Algorithm
After enabling the ETM algorithm, the X axis is commanded to make the same move. The new plot (Figure 4) shows a move and settle time of 202 ms. [Note: The analog input has not been reduced. The ETM algorithm does not reduce base motion, but only improves the ability of the servo to track it.]
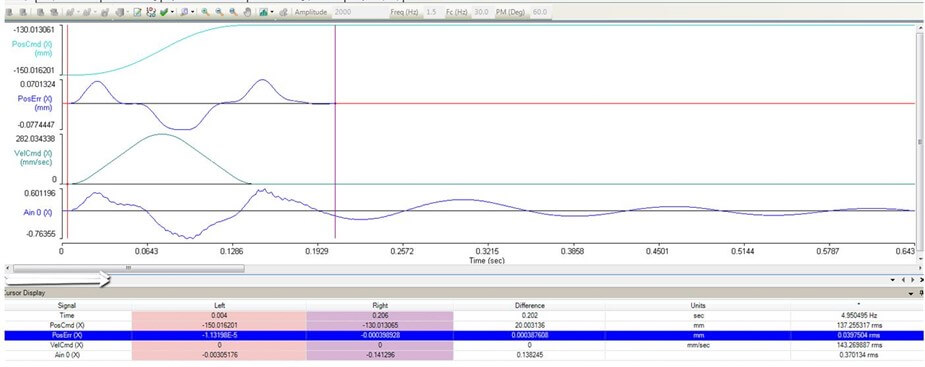
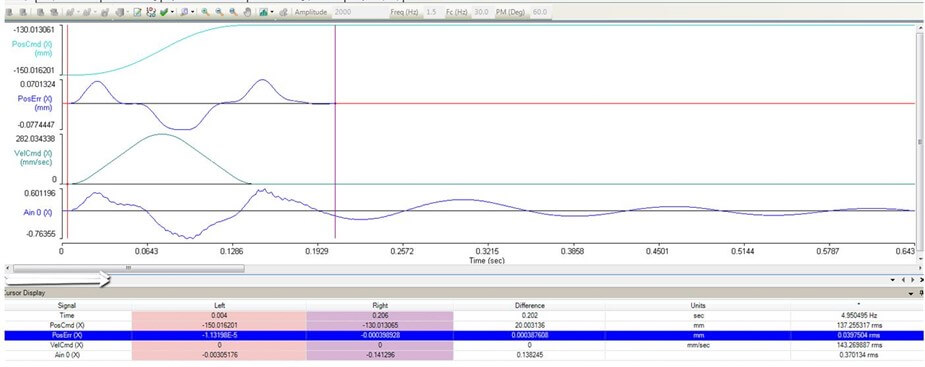
Comparing the two results, the time to complete the move is reduced from 340 ms to 202 ms.
Common Applications of ETM
ETM is used in many applications in the semiconductor, machine tool, and laser processing industries. ETM can be used to improve high dynamic performance positioning and reduce contouring error.
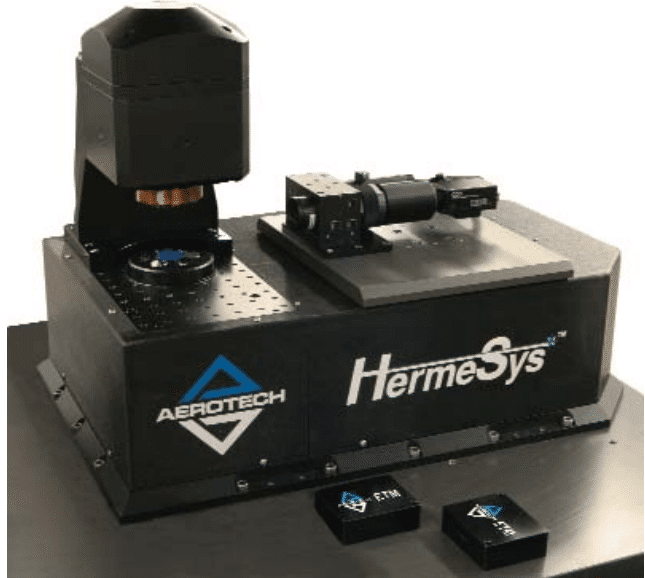
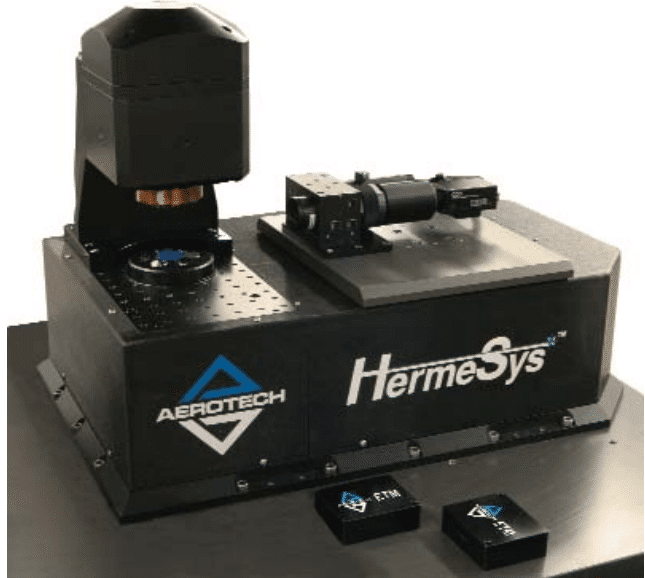
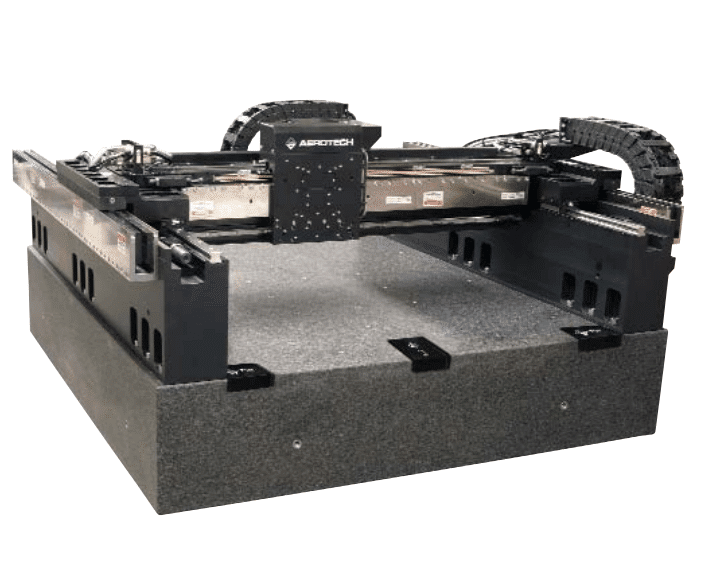
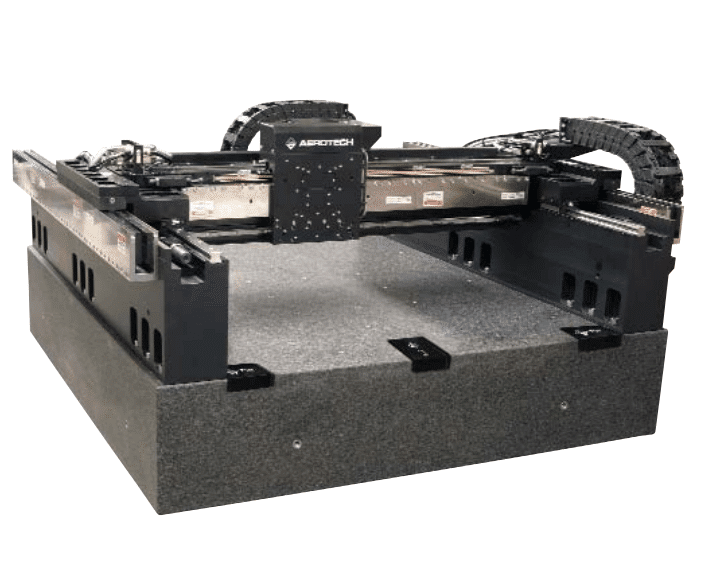
Summary
Aerotech’s ETM provides a low-cost solution for improving the productivity of new and existing machines with easy installation and no changes to existing mechanical hardware. Contact your local Aerotech representative to see how ETM modules can make your machine more productive.