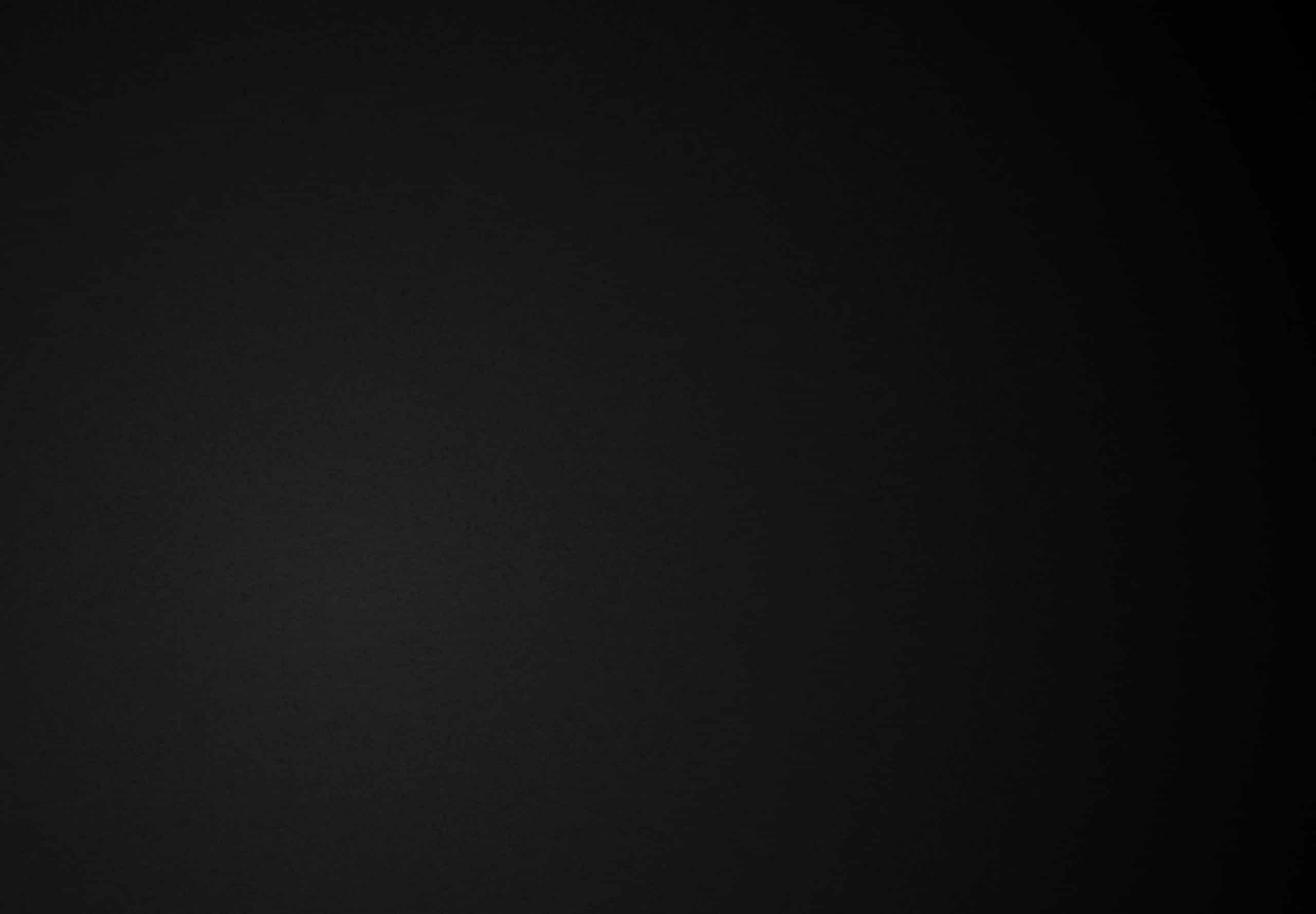
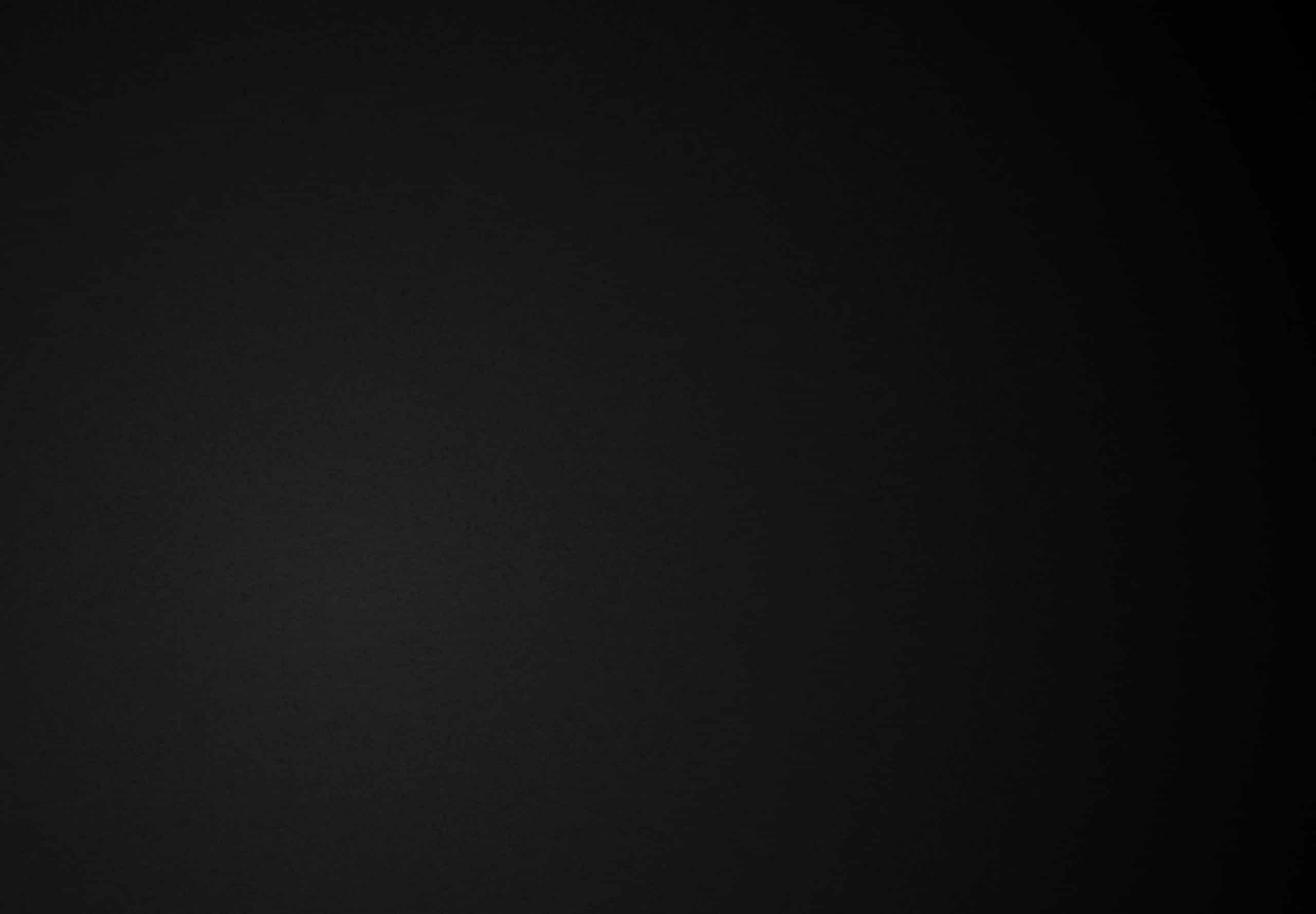
MOTION CONTROL PLATFORM SELECTION GUIDE
Meet your motion control match.
Compare our motion control platforms to determine which is the best fit for your needs.
Automation1 | Legacy | |
---|---|---|
Develop | Automation1 MDK Motion Control Development Kit Automation1 MachineApps |
Motion Composer Suite |
Control | Automation1 iSMC Intelligent Software-Based Machine and Motion Controller | A3200 Software-Based Machine Controller |
Drive | Servo Motor Hexapod* Galvo Scan Head |
Servo Motor – A3200, Ensemble, Soloist Galvo Scan Head – A3200 Piezo – A3200, Ensemble Hexapod – A3200 |
Connect | HyperWire Sockets Interface |
IEEE-1394/FireWire – A3200 AeroNet – Ensemble |
*Hexapods can be controlled by servo motor drives.
General Tools
Single Application for Configuring, Programming & Data Visualization | Yes | No |
Application-Wide User Management | Yes | No |
Deploy Custom Applications for Linux | Yes | No |
Advanced Controller File System | Yes | No |
All Controller Files Zip to Single Machine Controller Definition File | Yes | No |
Device Manager (Catalog Manager) | Yes | Yes |
Multiple Simultaneous Client Connections to a Controller | Yes* | No |
Controller History Tracking | Coming Soon | No |
Plug & Play Electrical & Mechanical Device Support | Future | Limited |
*note: Multiple simultaneous connections are possible via the Automation1 APIs. |
Available Add-On Applications and Software Tools
Motor Sizer (Free) | Yes | Yes |
Motion Designer | Future | Yes |
HexGen Hexapod Sizer | Yes | A3200 |
CADFusion | Yes | A3200 |
Galvo CFC (Free) | Yes | A3200 |
HMI Tool | Yes – MachineApps | A3200 – CNC Operator Interface |
Setup and Configuration Tools
EasyTune 1-Button Servo Tuning | Yes | Yes |
Axis Calibration | Yes | Yes |
Sine-Wave Encoder Tuning | Yes | Yes |
Loop Transmission/ Frequency Response Tool | Yes | Yes |
Advanced Diagnostics & Tuning | Yes | Yes |
System & Controller Performance Checking | Yes | No |
Drive Firmware Loading from Configuration Tool | Yes | No |
Automatically Configure Drive Communication Bus | Yes | No |
Machine Setup System Configuration Wizard | Yes | No |
Programming and Development
Programming Language | AeroScipt | AeroBasic | ||
Load, Compile & Run Programs | Yes | Yes | ||
Numeric Data Type | Yes | Yes | ||
String Data Types | Yes | Yes | ||
Global Variables | Yes | Yes | ||
User-Defined Functions | Yes | Yes | ||
Variables & I/O Watch | Yes | Yes | ||
Multi-Dimensional Arrays | Yes | Ensemble, Soloist | ||
Program & Local Variables | Yes | Ensemble, Soloist | ||
Structures | Yes | Ensemble, Soloist | ||
User-Defined Libraries | Yes | Ensemble, Soloist | ||
Intellectual Property Protection of Libraries | Yes | Ensemble, Soloist | ||
Intelligent Autocomplete IDE | Yes | No | ||
Real-Time Build Error Checking | Yes | No | ||
Axis Data Type & Axis Arrays | Yes | No | ||
Switch, Foreach & Break Statements | Yes | No | ||
CNC Functionality/RS-274 | Yes* | A3200 | ||
*note: G-Code was a paid option in the A3200 controller, but comes standard with an Automation1 controller. |
Data Collection and Visualization
1D & 2D Data Visualizer | Yes | A3200, Ensemble |
Fast Fourier Transforms (FFTs) | Yes | Yes |
Save System Data Directly to A File | Yes | Yes |
View 1D & 2D Data Concurrently | Yes | No |
HMI Software
Dedicated Application for Viewing HMI | Yes | A3200 |
Dedicated Workspace for HMI Development | Yes | No |
Build Simple Interfaces for Operators | Yes | No |
Apply Your Own Branding (Icons, Colors, Etc.) | Yes | No |
Design Several HMI Screens per Controller | Yes | No |
Execute Immediate Commands | Yes (can be hidden) | A3200 |
Abort & Reset Buttons | Yes (can be hidden) | A3200 |
Choose Your HMI Layout | Yes (user customizable) | No |
Build Several HMI Interfaces for Each Controller | Yes (user customizable) | No |
Camera Module (Video Feed) | Yes (user customizable) | No |
Data Visualizer Module (Digital Scope) | Yes (user customizable) | No |
Jog Pad Module | Yes (user customizable) | A3200 |
Message Log Viewer Module | Yes (user customizable) | A3200 |
Programming Module (Run & Debug Programs) | Yes (user customizable) | A3200 |
Task Status Module | Yes (user customizable) | A3200 |
Variables & I/O Module | Yes (user customizable) | No |
Axis Dashboard/Manager Module | Yes (user customizable) | A3200 |
Run Mode, Retrace Mode & Manual Feedrate Override (MFO) Module** | No | A3200 |
Tool Table Module | No | A3200 |
Access Control* | Yes | A3200 |
View Modal Status | Yes | A3200 |
Display Custom Messages | Yes | A3200 |
Deploy Several Jog Pads at the same time. | Yes | No |
State-Control of Button/Indicator Pages | Yes | No |
State Control of Customizable Pushbuttons | Yes | No |
Preview Button and Indicators in Design Tool | Yes | No |
Keyboard Shortcuts | No | A3200 |
Choose a Startup or Shutdown Program** | No | A3200 |
* Currently only available for MachineApps deployed to PC-based controllers. ** Currently there is no canned HMI functionality for this feature. This feature can be deployed via custom pushbuttons and/or AeroScript code. |
Controller Hardware
Industrial PCs | Automation1 iPC | n/a | A3200-iPC | |
Customer PCs | Yes* | n/a | A3200* | |
Intelligent Drive-Based Controller | n/a | Automation1 iXR3 Automation1 iXC6e Automation1 iXC4e Automation1 iXC4 Automation1 iXC2e Automation1 iXC2 Automation1 iXL5e Automation1 iXL2e Automation1 iXI4 |
Ensemble, Soloist** | |
*PC must meet Aerotech’s specifications and adhere to all required setup procedures. **See list of drive hardware below. |
General Features
Programmable Coordinated Motion Trajectories | Yes, 32 Axes | Yes, 12 Axes | A3200, Ensemble | |
Programming Tasks | 4 User Tasks (Std). 31 User Tasks (Opt.) 1 Reserved task |
4 User Tasks (Std). 9 User Tasks (Opt.) 1 Reserved task |
Varies | |
Connection Latency | Local: 1.0 msec Ethernet: 1.0 msec |
Ethernet: 3.3 msec USB: 4.2 msec |
Not specified. | |
Connection Bandwidth | Local: 87.0 MB/sec Ethernet: 41.0 MB/sec |
Ethernet: 10.5-11.7 MB/sec USB: 7.3-8.1 MB/sec |
Not specified. | |
PC-Based / Software Controller | Yes | n/a | A3200 | |
Drive-Based Controller | n/a | Yes | Ensemble, Soloist | |
Expanded IO Available | Yes | Yes | Yes | |
Dual Loop Control | Yes | Yes | Yes | |
Sinusoidal Commutation | Yes | Yes | Yes | |
Fast Position Capture | Yes | Yes | Yes | |
High-Speed Registration | Yes | Yes | Yes | |
On-the-Fly End-Point Modification | Yes | Yes | Yes | |
Data Acquisition | Yes | Yes | Yes | |
Joystick Support | Yes | Yes | Yes | |
Gantry Mode | Yes | Yes | A3200, Ensemble | |
Signal Logging | Yes | Yes | A3200 | |
Coordinate Transformations | Yes | Yes | A3200 | |
Motion Trajectory Scaling | Yes | Yes | A3200 | |
Motion Trajectory Translation | Yes | Yes | A3200 | |
Motion Trajectory Rotation | Yes | Yes | A3200 | |
Motion Trajectory Mirroring | Yes | Yes | A3200 | |
C-Based Kinematics* | Yes | No | No | |
AeroScript (Native Language) Kinematics | Yes | Yes | A3200 | |
3D Error Mapping | Yes | Yes | A3200 | |
Access Control | Yes | No | No | |
*Automation1 has a C programming language kinematic interface that enables both inverse and forward kinematics to be calculated. Please consult the factory about this capability. |
Calibration
1D Calibration File | Yes | Yes | Yes |
Accuracy Correction | Yes | Yes | Yes |
2D Calibration File | Yes | Yes | A3200, Ensemble |
Orthogonality Correction | Yes | Yes | A3200, Ensemble |
Straightness Correction | Yes | Yes | A3200, Ensemble |
ThermoComp – Thermal Compensation | Yes | Yes | A3200 |
Galvo Calibration & Power Factor Correction | Yes | n/a | A3200 |
Advanced Calibration | Coming Soon | Coming Soon | No |
Motion Features
Servo Motor Trajectory Calculation Rate | 20 kHz | 20 kHz | 8 kHz – A3200 1 kHZ – Ensemble, Soloist |
|
Galvo Scan Head Trajectory Calculation Rate | 100 kHz | n/a | 48 kHz – A3200 | |
Point-to-Point Motion | Yes | Yes | Yes | |
Contoured Motion | Yes | Yes | A3200, Ensemble | |
Arbitrary Path Generation (PVT Motion Commands) | Yes | Yes | Yes | |
Multiple Axis Homing Routines | Yes | Yes | Yes | |
Velocity Blending | Yes | Yes | Yes | |
Velocity Profiling | Yes | Yes | Yes | |
Electronic Gearing | Yes | Yes | Yes | |
Electronic Cam Profiling | Yes | Yes | Yes | |
Safe Zones | Yes | Yes | A3200 | |
Bezier Motion Commands | Coming Soon | Coming Soon | A3200 | |
Cutter Radius Compensation | Yes | Yes | A3200 | |
Lookahead | Yes | Yes | A3200 | |
Acceleration Limiting | Yes | Yes | A3200 | |
Corner Rounding | Yes | Yes | A3200 | |
Parts Rotation | Yes | Yes | A3200 | |
Retrace (Block-by-Block) | Yes | Yes | A3200 | |
Tool Normalcy Control | Yes | Yes | A3200 | |
SLICE Raster and Step Command* | Future | Future | A3200 | |
Ellipses (G-Code)* | Future | Future | A3200 | |
Work Offsets* | Yes | Yes | A3200 | |
Cutter Offset Compensation* | Coming Soon | Coming Soon | A3200 | |
Tool Tables | Coming Soon | Coming Soon | A3200 | |
*Automation1 includes the ability to write custom libraries. Several application-specific motion commands once handled natively by our controllers can now be accomplished via custom libraries. Our own libraries will be further developed over time. |
Advanced Motion Features
Enhanced Tracking Control | Yes | Yes | Yes |
Friction Compensation | Yes | Yes | Yes |
Command Shaping | Yes* | Yes* | Ensemble, Soloist |
Cross-Axis Feedforward | Yes* | Yes* | A3200, Ensemble |
Harmonic Cancellation | Yes* | Yes* | Yes |
Enhanced Throughput Module Support | Yes | Yes | Yes |
Gain Scheduling | Coming Soon | Coming Soon | Ensemble, Soloist |
* Requires the Dynamic Controls Toolbox configuration option to be added to the Automation1-iSMC at the time of order. |
Process Tool Control Features
Integrated Digital & Analog I/O Control with Motion Programming | Yes | Yes | Yes |
Position Synchronized Output (PSO) | Yes | Yes | Yes |
Part-Speed Position Synchronized Output (Part-Speed PSO) | Yes | Yes | A3200 |
Analog Power Control | Yes | Yes | A3200 |
Distance Logging | Coming Soon | Coming Soon | A3200 |
Galvo Scan Head Controller Features
Servo Control Rate | 200 kHz | n/a | 192 kHz – A3200 | |
Galvo Scan Head & Voice Coil Motor Support | Yes | n/a | A3200 | |
Infinite Field of View (IFOV) | Yes | n/a | A3200 | |
Drive Array for Process Control & Data Acquisition | Yes | n/a | A3200 | |
Barcode Datamatrix* | Coming Soon | n/a | A3200 | |
*Barcode generation is supported via Windows fonts in CADFusion application. |
Drive-Based Controller Hardware
Servo Drives with PWM Amplifiers and Motion Controller | PWM Drive-Based Controllers | PWM Drives |
Servo Drives with Linear Amplifiers and Motion Controller | Linear Drive-Based Controllers | Linear Drives |
Drive Racks | Drive Racks with Motion Controller | Drive Racks |
Servo Controllers with Motion Controller | Automation1 iXI4 | n/a |
Drive Hardware
Servo Drives with PWM Amplifiers | PWM Drives | PWM Drives |
Servo Drives with Linear Amplifiers | Linear Drives | Linear Drives |
Drive Racks | Drive Racks | Drive Racks |
Stepper Drives & Controls | Stepper Drives & Controllers | Stepper Drives & Controllers |
Galvo Scan Head Drives | Galvo Laser Scan Head Drives | Galvo Laser Scan Head Drives |
Dedicated Hexapod Controllers | Future | HEX RC |
Servo Controllers | Automation1 XI4 | Nservo Nservo-OEM |
Galvo Scan Head XY2-100 Interface | Automation1 GI4 | Nmark-SSaM |
Servo Motor Drive Features
Servo Control Rate | 20 kHz | 8 kHz – A3200 20 kHZ – Ensemble, Soloist |
||
PWM & Linear Amplifier Options | Yes | Yes | ||
AC Brushless, DC Brush, Voice Coil & Stepper Motor Support | Yes | Yes | ||
Hexapod Support | Yes | A3200 | ||
Backlash Compensation | Yes | Yes | ||
Rollover Mode | Yes | Yes | ||
Brake (Enable/Output/DisableDelay/EnableDelay) | Yes | Yes | ||
Analog & Digital I/O | Yes | Yes | ||
Drive Array for Process Control & Data Acquisition | Yes | Yes | ||
Safe Torque Off | Yes | No** | ||
Autofocus | Yes | Yes | ||
Analog Input to Servo Loop | Yes | Yes | ||
Fiber Optic Alignment Routines | Yes*** | A3200 | ||
Tool Center Point Programming Control | Yes*** | A3200 | ||
Touch Probe Routines | Yes | A3200 | ||
Velocity Mode | Yes | Soloist | ||
Torque Mode | Yes | Soloist | ||
Barcode Datamatrix | No**** | A3200 | ||
*The Automation1 servo controller operates off of a 20kHz trajectory from the controller. Ensemble and Soloist have servo controllers that interpolate up to 20 kHz of servo control points from a 1 kHz trajectory. **These drives include an E-stop Sense input that alarms the drive of an external e-stop condition. *** Requires the AeroScript Plus configuration option to be added to the Automation1-iSMC at the time of order and for the desired routines to be purchased via the AeroScriptPlus product configurator. ****Barcode generation is supported via Windows fonts in CADFusion application. |
Supported Feedback Devices
None (Open-Loop) | Yes | Yes |
Square-Wave Encoder | Yes | Yes |
Single-Wave Encoder | Yes | Yes |
Analog Input | Yes | Yes |
Half-Effect Switches | Yes | Yes |
EnDat Encoder | Yes | Yes |
Biss Encoder | Yes | Yes |
Resolver | Yes | Yes |
SSI Encoder | Yes | No |
Dual Loop | Yes | Yes |
Dual-Loop with Sine-Wave Encoders | Yes | No |
General Specifications
Motion Control Bus | HyperWire® | FireWire – A3200 AeroNet – Ensemble |
||
Physical Layer | Glass Optical Fiber | IEEE-1394 – A3200 Ethernet – Ensemble |
||
Communication Rate | 2 Gbps | 400 Mbps – A3200 12.5 Mbps – Ensemble |
||
Jitter* | <1 nsec | 60 – 680 nsec – A3200 20 – 180 nsec – Ensemble |
||
Master Clock Stability | +/- 5ppm | +/- 100 ppm – A3200 +/- 50 ppm – Ensemble |
||
Maximum Network Rate | 100 kHz | 8 kHz – A3200 1 kHz – Ensemble |
||
MIMO Communication Support | Gantry Control over HyperWire | No – A3200 No – Ensemble |
||
*Patented jitter reduction technology nearly eliminates drive-to-drive jitter and maintains constant low jitter for variable numbers of hardware devices on the communication bus. |
Library Support
.NET | Yes | Yes |
C | Yes | Yes |
C++ | Yes | Yes |
LabVIEW VIs | Yes | Yes |
MATLAB API | Coming Soon | Yes |
EPICS | Yes | Yes |
TANGO* | Yes | Ensemble, Soloist |
Python | Yes | No |
REST API | Future | A3200, Ensemble |
*note: please consult the factory for TANGO support. |
Industrial Bus Support
EtherCAT | Yes* | A3200** |
Modbus TCP | Yes*** | Yes |
EtherNet/IP | Coming Soon | Ensemble, Soloist |
Web Server | Future | A3200 |
Ethernet TCP/IP | Future | Yes |
PROFINET | Future | A3200 |
RS-232 | No | Yes |
*EtherCAT slave on drive-based controllers only. **EtherCAT I/O master on PC-based controllers only. ***Fully supported for PC-Based controllers. Supported for drive-based controllers as a beta feature. |
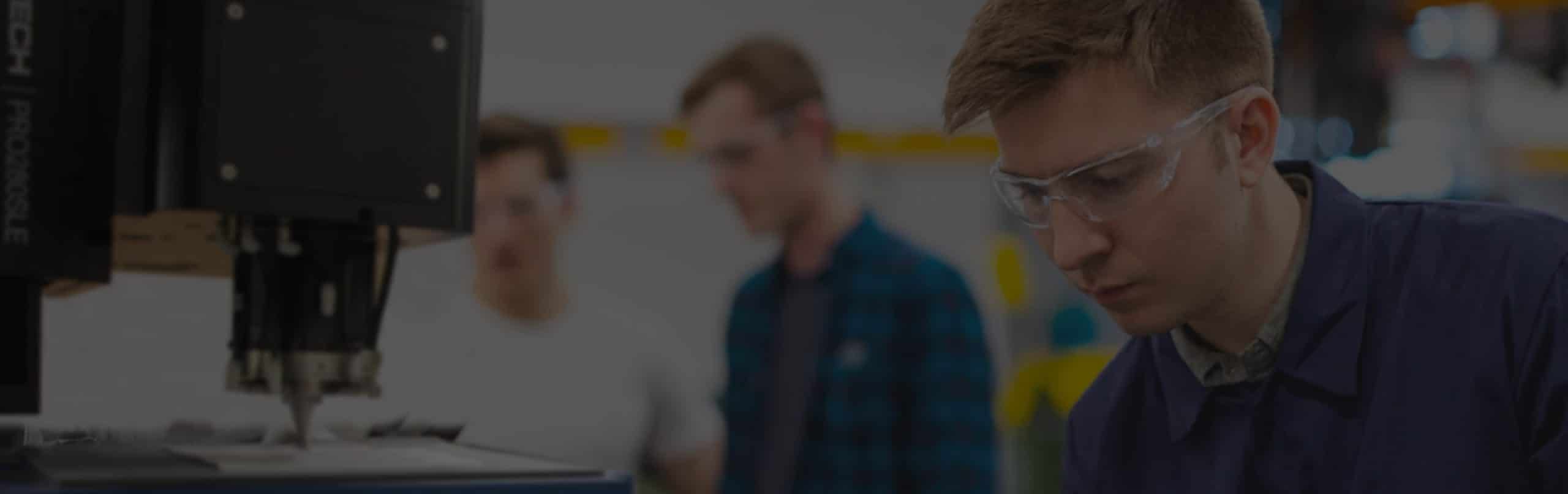
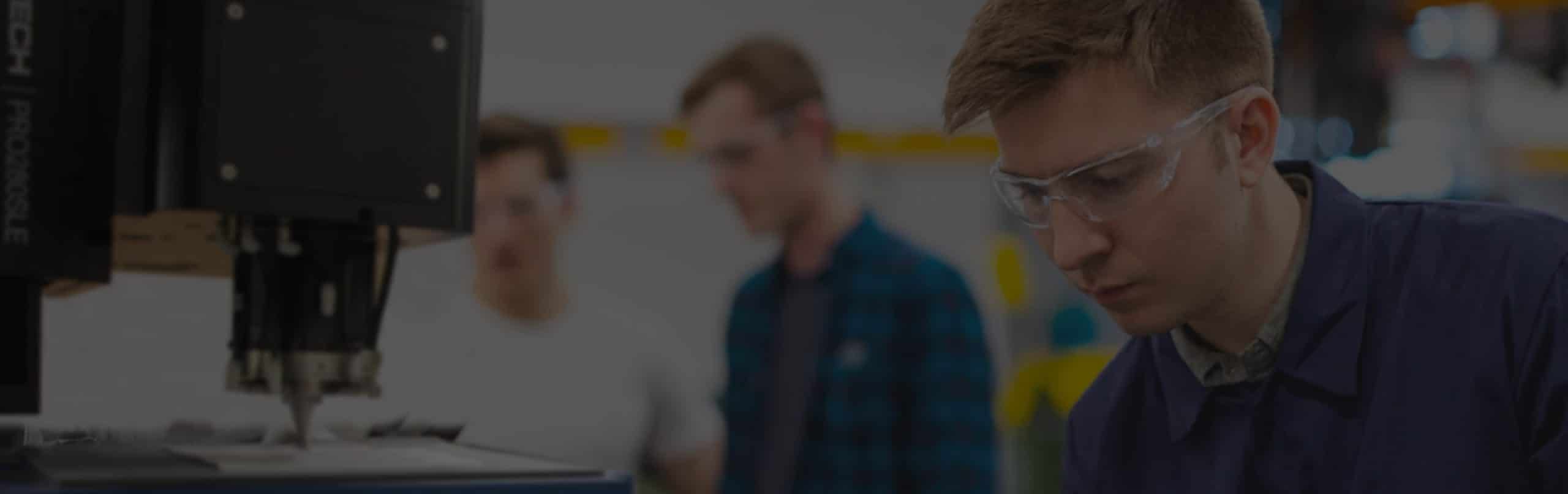