Application Note, Custom Engineered Motion Systems, Gantries, Gimbals & Optical Mounts, Hexapods, Motion Control Platforms, Piezoelectric Nanopositioners, Science & Research Institutions, Stages & Actuators
Application Note
New Data Collection Tool for Complex Positioning Systems at Beamlines
Maximizing measurement throughput is paramount in scientific and industrial applications alike, which is certainly the case with beamline and synchrotron facilities. Beamline and synchrotron facilities allot time to users with the understanding that users will collect all of their data in a given period. A hindrance to this was the slow data collection process implemented at many of these facilities, and this meant allocating more time to each user. What if the data collection process was faster? What if samples and chemical reactions could be measured on the fly while the data collection was instantaneously triggered in the background? Aerotech developed a tool for these cases, and it collects more data with more throughput on even the most complicated sample manipulation platforms.
In beamline and synchrotron applications triggering data collection has historically been a synchronized process while the sample is manipulated within the beam’s cross section. A positioning system would move the sample to be tested an incremental distance, a set amount of time would go by to make sure the sample settled into its commanded position, and then the data collection process would be triggered. This was time consuming and cumbersome. To solve this problem Aerotech developed a Position Synchronized Output (PSO) feature-set based on real-time position feedback data. As the sample was moved the high-speed controller could trigger and collect data based on real-time position feedback data without halting the motion. This enabled sample scanning and instantaneous high-accuracy data collection that was not previously possible. Continuously moving the sample throughout the measurement process improved throughput and allowed beamline scientists to run more tests and collect more data than ever before.
This powerful position-based scanning feature has led to new challenges in regard to complex positioning systems at these facilities that do not rely on 1:1 kinematic configurations. Specifically, they use transformational equations and virtual (non-real) axes to command physical (real) axes to move. This means that the data collection is now tied to a virtual command instead of a physical high-speed feedback channel of a real axis. This makes the position-based data collection triggering system unsuitable since it no longer has access to the physical high-speed position feedback through the virtual axes.
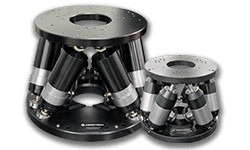
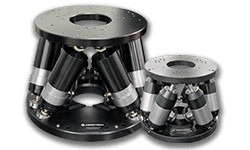
To solve this latest challenge, Aerotech has introduced a new Part-Speed Position Synchronized Output (PSO) feature. This feature allows a user to program in kinematic arrangements not previously possible while still gaining the scanning capabilities of position-based data collection. Part-Speed PSO triggers data collection based on the vector velocity command of the positioning system. This enables the PSO feature on any device using kinematic transformations for positioning, most notably for beamline and synchrotron facilities using the hexapod parallel kinematic platform. Hexapods do not accept the traditionHex Groupal position-based data collection approach since they require kinematic transformations to operate. The user programs in XYZ space, but the real hexapod moving axes are in a different coordinate system. With Part-Speed PSO, hexapods can now be used in these advanced data collection processes. Removing the need to step and settle before collecting data allows the powerful flexibility and scanning capability of a hexapod to be fully utilized.
Increasing measurement throughput using scanning has now reached the world of complicated parallel kinematics thanks to Aerotech’s new Part-Speed PSO feature.